Funktionsweise SLS
Selektives Lasersintern (SLS) ist ein pulverbasiertes Schmelzverfahren, wobei das Werkstück (3D Druckobjekt) in einem Pulverbett mit fast 100% Dichte isotrop gefertigt wird.
Im ersten Schritt wird eine hauchdünne Pulverschicht auf eine Bauplattform mittels eines Rakels oder einer Walze aufgetragen. Ein Laserstrahl verschmilzt im zweiten Schritt das aufgetragene Pulver punktgenau an den Stellen, die von der geladenen Druckdatei vorgegeben sind. Anschließend senkt sich die Bauplattform in einem dritten Schritt ab und es wird erneut eine komplette Pulverschicht aufgetragen.
Diese 3 Schritte wiederholen sich so oft, bis das gewünschte Bauteil komplett gefertigt ist, wobei die einzelnen Schichten an den definierten Stellen durch den Laser miteinander verschmolzen werden.
Das Verfahren ist sehr produktiv und genau. Zudem ist es kosteneffizient und sehr gut für Kleinserien geeignet, wo es teilweise bis zu 5.000 Stück Losgröße kostengünstiger als Spritzguss ist.
Als Material kommen Polyamid 12 (PA12), Polypropylen (PP) oder auch Thermoplastische Elastomere (TPE) zum Einsatz.
Oberfläche
Auflösung bis 0,2 mm
(Toleranz 0,2 %)
Bauraum bis 700 x 380 x 580 mm
Stückzahl / Kosten
genaues Fertigungsverfahren geeignet für Stückzahlen bis zu 5000 Stück
Material
Sintern von: Polyamid 12 (PA12), Polypropylen (PP), Thermoplastische Elastomere (TPE)
Einsatzgebiete
mechanisch hoch belastbare und isotrope Druckobjekte
z.B. Lagerbuchsen, Zahnräder, Gehäuseteile
Sehr gute Alternative zum Spritzguss bei Kleinmengen -> schnell und deutlich preiswerter
Oberflächenbeschaffenheit - Selektives Lasersintern
Die natürliche unbehandelte Oberfläche von im SLS Verfahren 3D gedruckten Bauteilen aus Polyamid zeigt eine matte Optik und ist leicht porös. Bei Bedarf kann eine glattere Oberfläche mittels weiterer Bearbeitungsschritte hergestellt werden. Chemisches Glätten oder eine Lackierung sind geeignete Verfahren, um eine signifikante Glättung zu erreichen und gegebenenfalls gleichzeitig andere Eigenschaften des 3D Druckes zu verbessern. Beispielsweise können mittels einer Lackierung die UV-Beständigkeit, Stoßfestigkeit und chemische Resistenz gegenüber Säuren erreicht werden.
SLS 3D Druckbeispiele - Polyamid PA12
Konstruktionsempfehlungen SLS
Toleranzen
-
Die Toleranzen sind abhängig vom verwendeten Material und der Bauteilgeometrie. In den meisten Fällen kann von diesen Werten ausgegangen werden:
• 0 – 30 mm: +/-0,2 mm
• Ab 30 – 100 mm: +/-0, 3mm
• Ab 100 mm: +/- 0,3 % des Nennmaßes
Wände und Stäbe
- [X/Y] Minimal mögliche Wandstärke = 0.6 mm
- [Z] Minimal mögliche Wandstärke = eine Schicht; Standard: 0,1mm
- [Stäbe] Minimale Stabstärke = 1 mm
Lose Verbindungen
- 0,3 mm abstand für lose Verbindungen
- Ohne Spalt zwischen einem männlichen und weiblichen Bauteil entsteht eine Presspassung
- Gilt nur für Bauteile die nach dem Bauprozess montiert werden! Ansonsten siehe Abschnitt Gelenke.
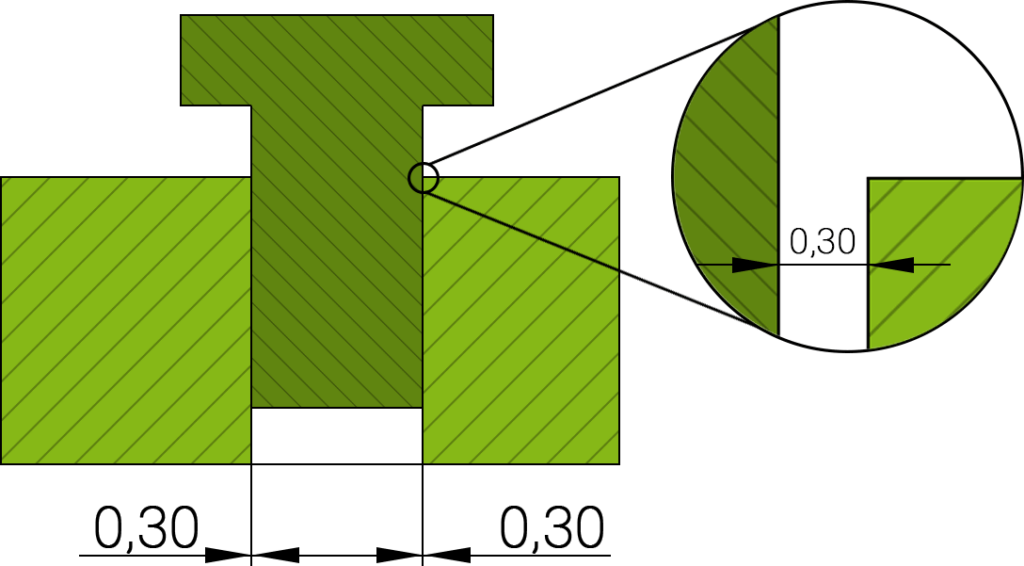
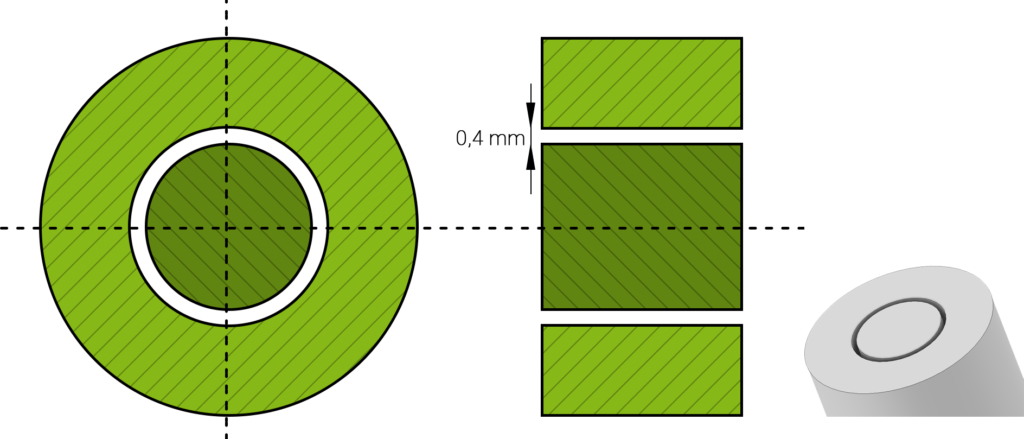
Gelenke
-
Spaltmaße (A) für Gelenke:
• x/y: 0,3 mm – 0,5 mm
• z: 0,5 mm – 0,6 mm
Stufen im Bauteil
- Wenn eine Bauebene mit einem Winkel von unter 20 ° zur x/y Ebene ausgerichtet ist, sind auf der Oberfläche eindeutig Stufen zu erkennen
- Je steiler der Winkel, desto feiner die Stufen. Die Sichtbarkeit ist auch von der Schichtdicke abhängig.
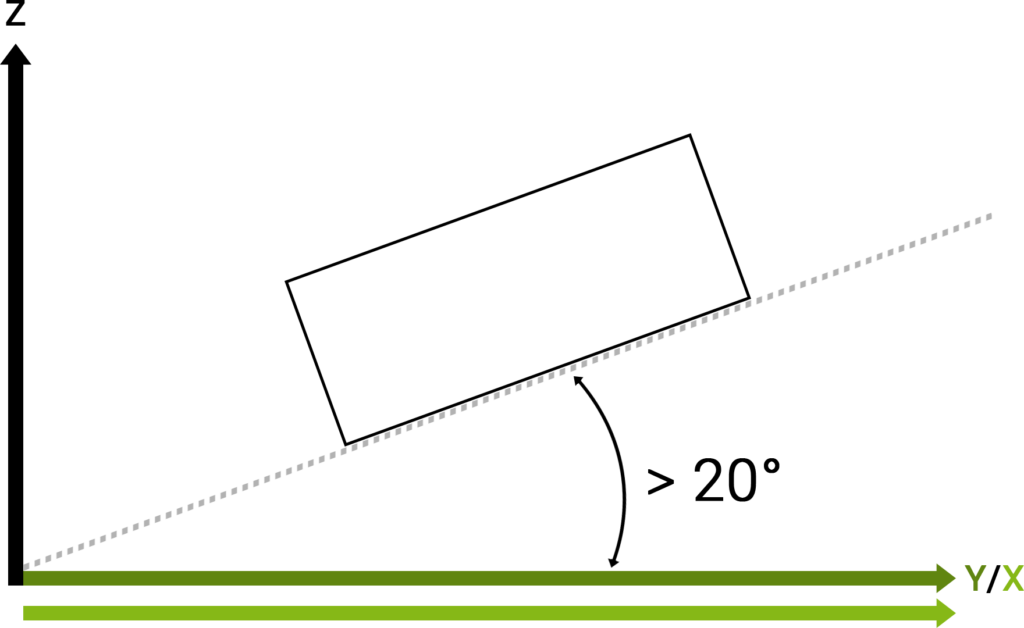
Kosten
- Kosten sind von der Bauhöhe (z-Richtung) abhängig (Maschinenstunden und Pulververbrauch)
-
Verkleinerung der Bauhöhe
• Bauteile mit möglichst geringer Höhe konstruieren
• Stapeln -
Reduktion des Bauvolumens
• Integrierte Konstruktion
• Leichtbau Konstruktion
• Kraftflussoptimierte Konstruktion
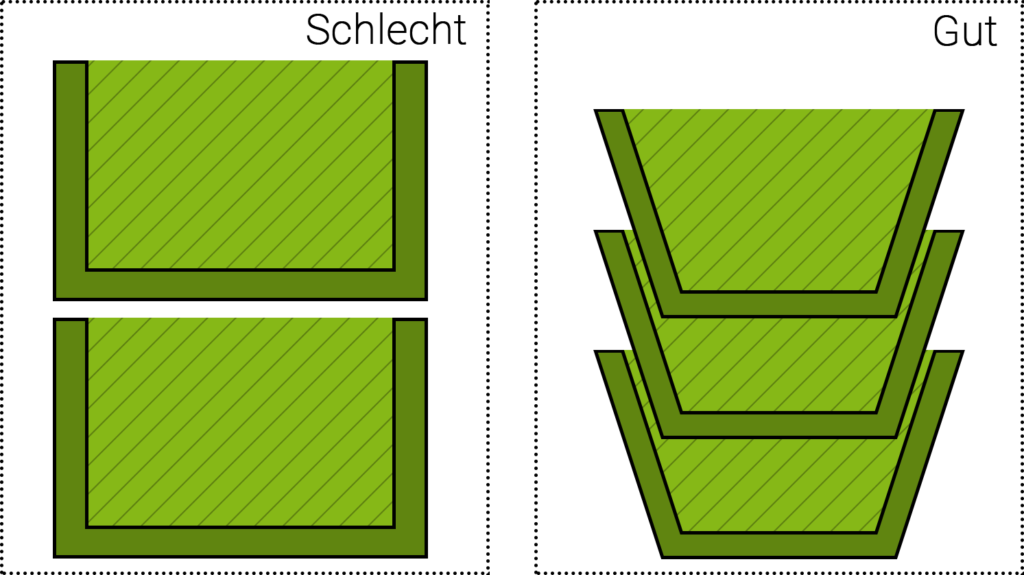
Schriftgröße
- Minimale Schriftgröße: 14 (für alle Baurichtungen)
-
Kleinere Schriftgrößen sind möglich aber abhängig von:
• Baurichtung
• Tiefe (bei negativen Schriftbild)
• Höhe (bei positiven Schriftbild)
Mindestdurchmesser von Aussparungen
- Minimaler Durchmesser: 1,0 mm
- Löcher mit einem Durchmesser von weniger als 1,0 mm können sich beim Drucken verschließen!
Austrittslöcher
- Eingeschlossene Hohlräume bleiben mit ungesintertem Pulver gefüllt, wenn keine entsprechenden Austrittslöcher vorhanden sind. Für optimale Ergebnisse sollten mindestens 2 Austrittslöcher mit einem Durchmeser von 3,5 mm oder mehr angelegt werden.
- Mehr und größere Austrittslöcher erleichtern das Entfernen von ungesintertem Material aus innereren Hohlräumen. Der Zugang für das Reinigungswerkzeug wird erleichtert.
- Für die angelegten Löcher kann ein entsprechender Verschluss (Stopfen) im gleichen Vorgang mitgedruckt werden.